Corrosion is a significant issue directly impacting the quality and durability of steel structural constructions. To address this situation, painting has proven to be the most effective solution and is widely applied in contemporary construction. Join Pebsteel in exploring the standardized steel structures painting process in the following article.
See more: Erection of Steel Structures
1. Why is it necessary to paint steel structures?
Steel structures are extensively utilized in daily life and across various sectors such as civil construction, industry, and telecommunications. However, steel is inherently susceptible to corrosion under the influence of normal environmental conditions. Consequently, to ensure the longevity of steel structures, the application of a paint coating on the surface is imperative to shield components from the impact of external environmental factors. Presently, executing the painting process on steel structures is not only a prevalent choice but also the most cost-effective solution. This method is widely applied in the construction of warehouses and the assembly of prefabricated steel-framed structures.
See more: What Is Structural Steel Welding? Definition And Methods
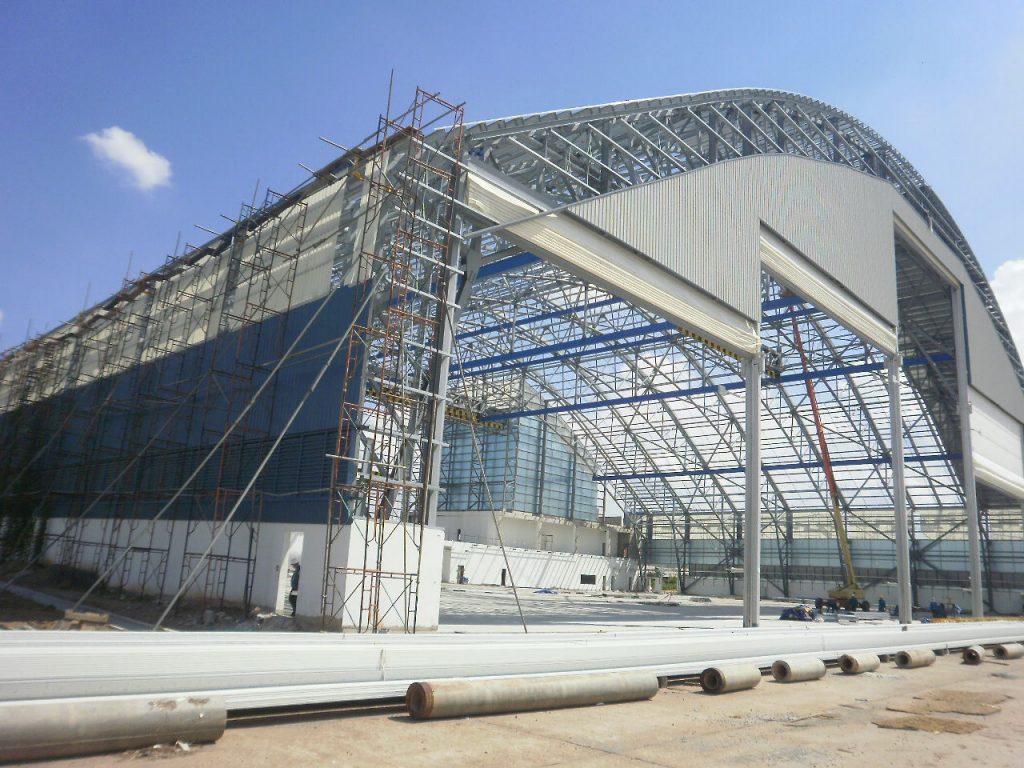
Paint coatings are the widely employed methods in the construction of warehouses and the implementation of prefabricated steel-framed structures.
2. What are the types of steel structures painting?
Paint coatings for steel structures can be categorized into three main types: Alkyd paint, Epoxy paint, and Polyurethane (PU) paint.
2.1. Alkyd Paint
Alkyd paint is an oil-based paint commonly applied to coat steel structure components. The primary component of this paint is Alkyd rust-resistant resin, a chemical compound derived from plants known for its strong adhesive properties. Additionally, this paint dries relatively quickly, exhibits excellent rust corrosion resistance, and maintains high color durability even in corrosive environments.
2.2. Epoxy Paint
Epoxy paint is a premium-grade coating composed of two main components: solvent and polyamide hardener. It can be utilized for both new and existing steel structures. However, its adhesion properties are not as robust as those of Alkyd paint. Therefore, emphasis must be placed on thorough cleaning and surface abrasion of the steel structures to ensure the paint film remains intact and free from peeling and cracking. In contrast to Alkyd paint, Epoxy paint cures and hardens within a few hours after the two components are mixed. Hence, it is advisable to mix only the amount of paint necessary for application within the paint’s working life to avoid wastage.
2.3. Polyurethane Paint
Polyurethane paint, commonly known as PU paint, is employed for long-term protection of various equipment, steel structures components for interior and exterior applications, industrial storage tanks, underground pipe systems, air ducts, bridge structures, ships, and various other construction projects. It boasts numerous advantages, including rapid drying, a durable surface, excellent resistance to impact and abrasion, corrosion resistance, strong adhesion, UV resistance, resilience to solvents, and chemical resistance, coupled with a diverse range of color options.
See more: The Solutions To Prevent Factory Roof Leaks
3. The most standardized painting process for steel structures
3.1 Step 1: Selection of an appropriate construction method
Depending on the surface characteristics of the steel structures and the surrounding spatial conditions, contractors may consider selecting an appropriate paint coating method. The following are the three most common methods:
- Brush Painting: Applicable to steel surfaces with irregularities, such as pits, various protrusions and recesses, weld areas, corners of steel beams, and joints of multiple steel sheets. These locations necessitate the use of brush painting, involving the application of paint with a brush, beginning with the first anti-corrosion coat, followed by subsequent paint layers.
- Roller Application: Used on materials with high viscosity, requiring good leveling properties and a flat surface before applying the primer coat. When applying multiple layers for the appropriate thickness, it is essential to use a roller of suitable size and type based on the dimensions of the steel beams. Typically, the rolling method is not recommended for applying anti-corrosion primer coats.
- Spray Gun Application: This versatile method can be applied to any steel structure but has limitations in confined spaces. Painters need to ensure factors such as paint viscosity, nozzle type, spray pressure, material temperature, distance from the spray nozzle to the surface, and spray angle to create a continuous and uniform paint film.
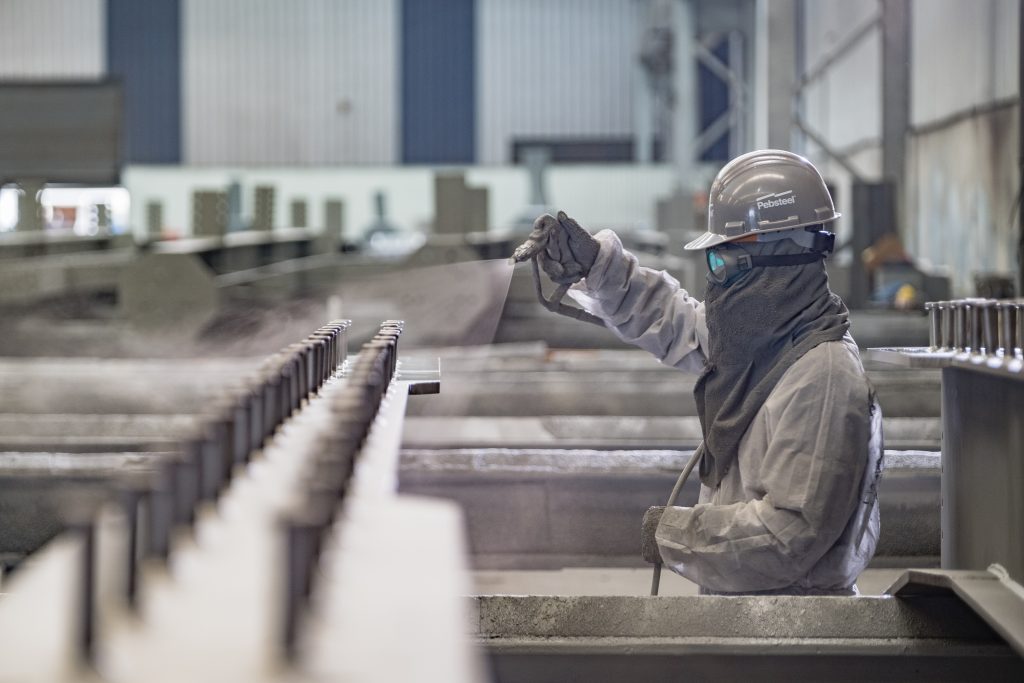
3.2. Step 2: Preparation and surface treatment of steel structures
In this phase, the technician employs a grinding machine in conjunction with an industrial dust extractor to cleanse the surface of the steel structures. Subsequently, the removal of contaminants such as oil, grease, dust particles, steel scale, and sea salt and the rectification or repair of severely damaged areas, including the mitigation of cracks, are undertaken.
For components with intricate surfaces, manual cleaning may be done using abrasive paper, scraping tools, or iron brushes. Conversely, for larger steel structures, additional equipment, such as wet sandblasters, shot blasting machines, etc., becomes necessary.
See more: 5 Ways To Reduce The Heat On Corrugated Iron Roof
3.3. Step 3: Application of primer coatings
Initially, it is imperative to open the paint container and stir the paint thoroughly for 2 to 3 minutes, optionally incorporating a suitable solvent to facilitate the paint coating process. A brush, roller, or spray gun is then used to ensure even distribution of pain across the surface with a film thickness of 40µm. Finally, the drying time is approximately 6 to 12 hours, depending on the type of paint, before proceeding with the application of the topcoat.
3.4. Step 4: Application of top coatings
The paint mixing process may be various, depending on the type of paint coatings used. Following the paint mixing, the painter will employ a brush, roller, or spray gun for the application phase. A uniform layer of the paint coating is initially applied to the surface, followed by multiple passes in two perpendicular directions. The painter must ensure an even application with a film thickness of 40µm (for Alkyd paint) or 100µm (for Epoxy paint) per layer. Two paint coating layers are applied, each spaced 4 to 8 hours apart. Furthermore, before the final layer, the surface needs to be cleaned and abraded.
See more: Corrosion Prevention Solution for Prefabricated Fertilizer Warehouse
3.5. Step 5: Inspection, error rectification, and project handover
Once the paint coatings on the steel structures have completely dried and are accessible for inspection, the painter will conduct a thorough examination and address any defects through the remedial method of puttying and filling. Ultimately, the project is handed over upon the completion of the surface finishing.
4. Conclusion
The above information is the most standardized process for painting steel structures and relevant information. Please contact Pebsteel by phone at +84 908 883531 or by email immediately at Marketing@pebsteel.com.vn if customers require comprehensive solutions for pre-engineered steel buildings and steel structures.