The acceptance of steel structures is a critical phase that determines whether the quality of the construction is assured for commissioning. Nowadays, the acceptance process must strictly adhere to current standards. Let’s delve into the regulations and technical requirements of the acceptance process for steel structures according to TCVN 170:2007 with Pebsteel in the following article.
See more: Mechanical Factory Design Standards and Procedures
1. The acceptance standards for steel structures
The construction of steel structures, particularly prefabricated steel buildings, is completed through the erection of various components. Consequently, the entire steel structures are closely interrelated. Strict adherence to acceptance standards is imperative to ensure the quality, safety, and durability of the construction.
See more: Erection of Steel Structures
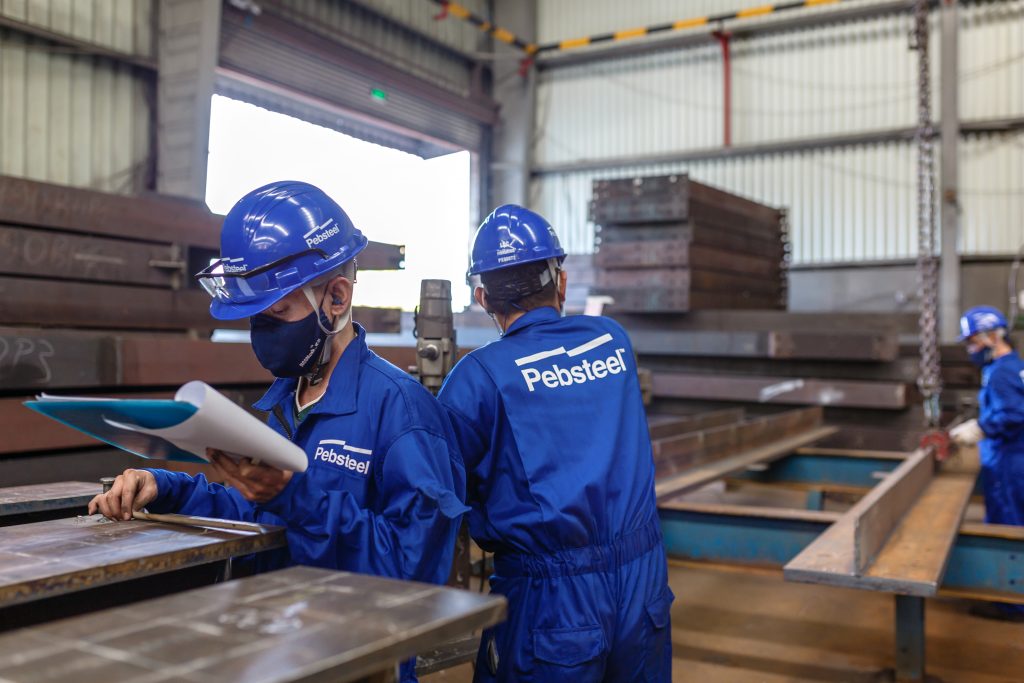
Here are the acceptance standards for steel structures according to TCVN 170:2007:
- Before being shipped, each structure must undergo inspection by the technical experts of the manufacturing unit.
- During the acceptance process, the parameters of the components must align with the standard requirements. These standards or technical guidelines are applied to specific components and design documents.
- For the mass-produced structures, the quantity, method, and inspection plan (including sample selection) must be established based on standards or technical guidelines specific to each structure.
- In the case of single-unit production and small quantities, the measurement and inspection plan (including sample selection) must be clearly defined in the designed document.
- Input, manufacturing inspection, and acceptance processes must adhere to the target list and measurements specified in Table 1 below, which should be based on the quality requirements of the components and the specified operating conditions.
- The results of the input material, manufacturing process inspection, and acceptance process must be recorded in the technical inspection documents or other relevant records. The measured parameters must be documented in the aforementioned records and must comply with the design document requirements for the structure.
Table 1: Types and parameters of inspection
Types of inspection | Parameters of inspection |
1 | 2 |
Input | Information on the quantity and specifications of composite details, input materials, and blanks encompassing factors such as steel type and code, geometric type and size, paint type, welding, and corrosion-resistant materials. This also includes information about the gas volume required for welding and cutting metal, as well as details about bolt types, nuts, etc. |
Fabrication | Geometric dimensions of shanks, molds, and other tools. |
Geometric dimensions of components and blanks, including dimensions after mechanical processing. | |
Composition of components or details before the welding process. | |
Number of welds and bolted connections. | |
Quantity of separately manufactured components in a structure. | |
Geometric dimensions of the components. | |
Corrosion protection weight, including the surface preparation process for anti-rust paint and coatings. | |
Acceptance | |
3.1 Periodic inspection and testing. | Parameters of the manufacturing technology. |
Stability inspection of the construction process and guarantee against the workload of inspecting input materials during the construction process. | |
Erection tests of the structures based on the combination. | |
Load-bearing capacity and stiffness. | |
3.2 Inspection and Handover | Ensure the completeness of document inspection for both input and in-process materials, as well as ensure compliance with guidelines and requirements in technical documents. |
Evaluate the geometric parameters of the components and determine the impacts on the composite equipment erection process. | |
Visual inspections of components | |
Combination inspections, corrosion protection, welds, and other requirements according to standards, technical specifications, and other design documents. | |
Labeling, packaging, and erection. |
Note:
- The examination of the composite capability, load-bearing capacity, and stiffness of the components must be conducted rigorously, especially when they are stipulated in standards, technical guidelines, and documents designed for each specific structure.
- The diagnostic process will be conducted by external observation to verify compliance with standard requirements and identify potential locations of defects in the component.
See more: The Process Of Structural Steel And Plate Fabrication
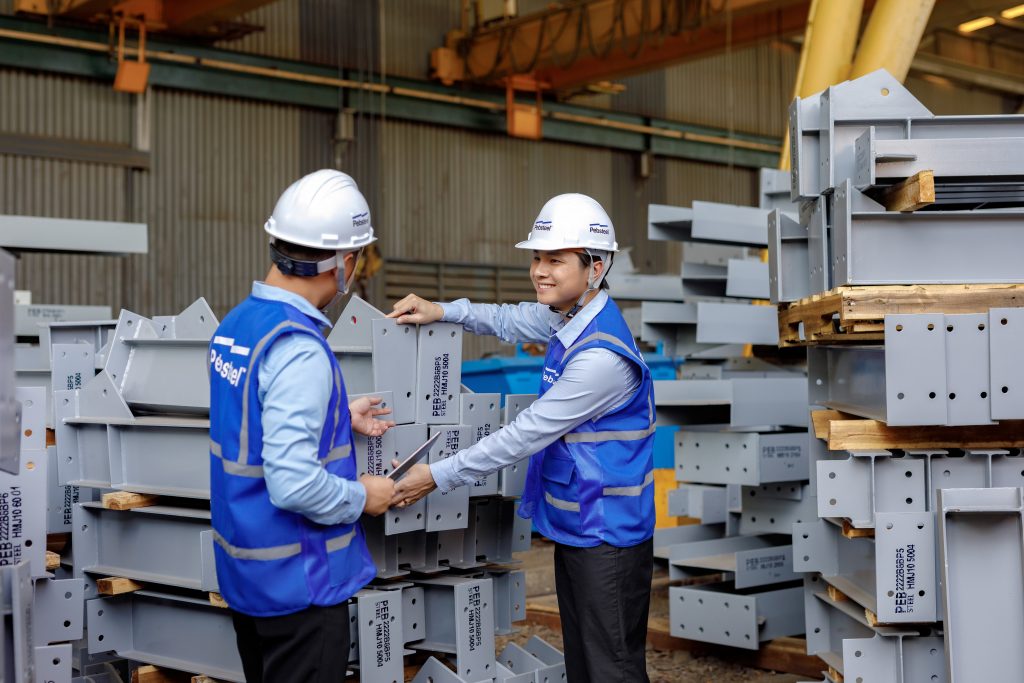
2. The acceptance process for steel structures
The contractors organize the internal acceptance process and subsequently generate the acceptance request form for submission to the investor. Investors then conduct the acceptance process based on the provided request form from the contractors. The activities that need to be executed during the acceptance process include:
- Reviewing the documentation provided by the contractors to support the acceptance process.
- Inspecting the subject of the acceptance process on-site or in the production workshop.
- Assessing the suitability of details, components, or structures regarding the design, construction standards, and technical guidance documents.
- Allowing the continuation of the next working phase upon the completion of the acceptance process
The acceptance process is required to be documented in the acceptance report. Individuals directly involved in the acceptance process must sign and provide their personal information in the report.
See more: Common Types Of Structure Steel In Construction
3. Conclusion
These are the latest acceptance standards and acceptance process for steel structures based on TCVN 170:2007. For comprehensive solutions related to pre-engineered steel buildings and steel structures, please contact Pebsteel by phone at +84 908 883531 or by email immediately at Marketing@pebsteel.com.vn.